Problem definition
Every industrial process is often a complex layered system of production which has been developed for years and there simply hasn’t been enough time for everyone to adapt to the digital climate we have today. Often times, even the processes that do work aren’t nearly optimal, and those that break-down are doing so due to the lack of control and information. The most impactful part of each issue is the human problem, the human tendency to fault and to misinform in everyday situations, while a digital solution is built precisely to avoid that. Using web and mobile technologies, we were able to build a usable alternative for each step in the human intervention in a singled-out layer of a process.
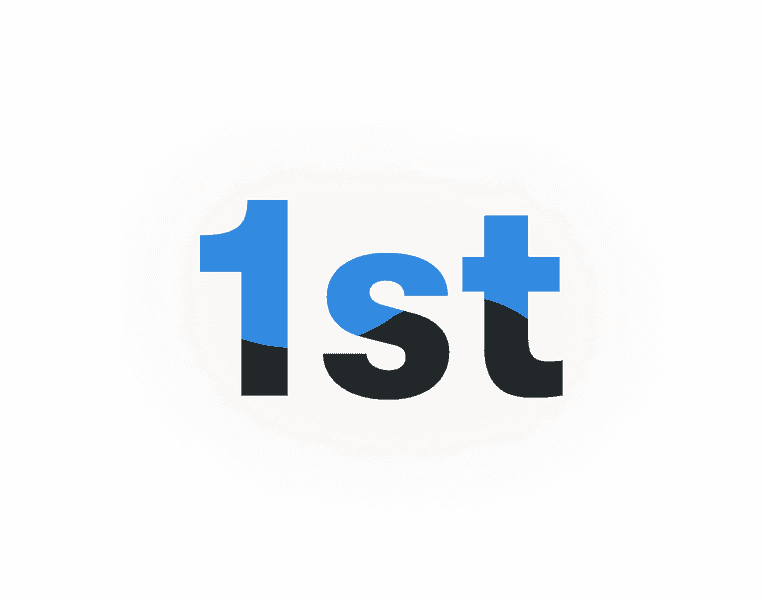
Information Gathering
Getting to know the inner workings. Process information is often segmented into multiple formats and is hard to access, process, and understand. This information determines the data structure being created and stored.
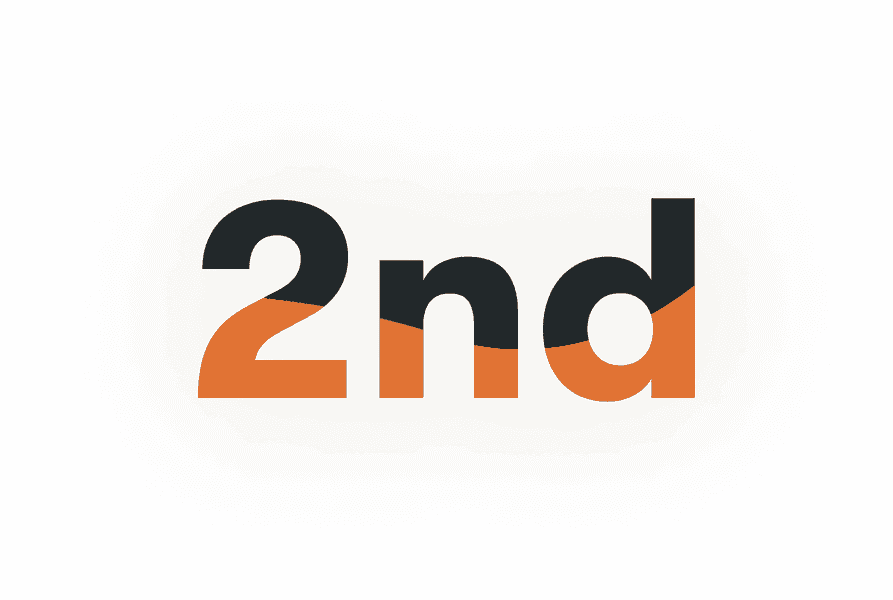
Layering of a process
Multiple steps & multiple people. Each layer in the process creates an additional level of complexity and is an opportunity for fault to commence. Issues range widely from communication errors to non-representative data. Understanding the status quo is the key to transformation.
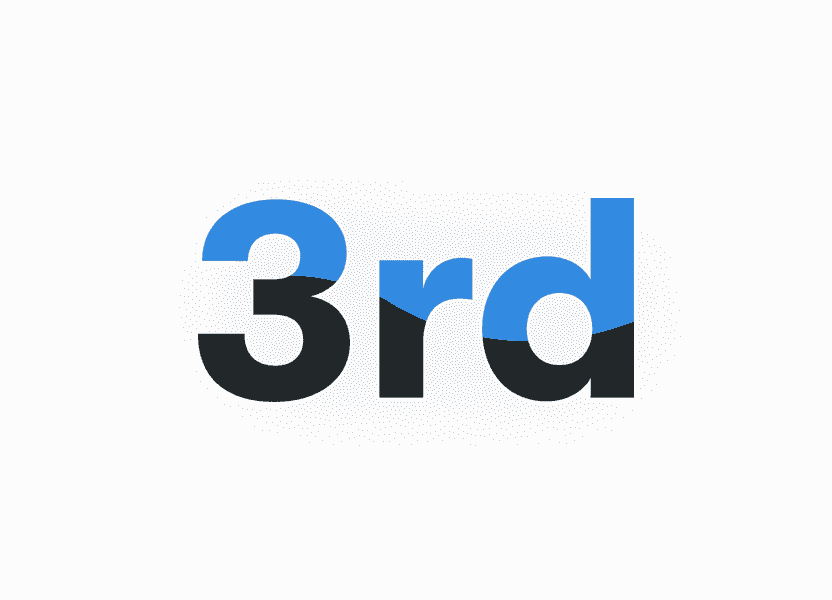
Data Transmission
Paper problem. Something is wrong if a printed piece of paper is going around the office or production area. Not only are there ecological implications, but there is little-to-no control present. Moreover, the information is temporary until discarded.
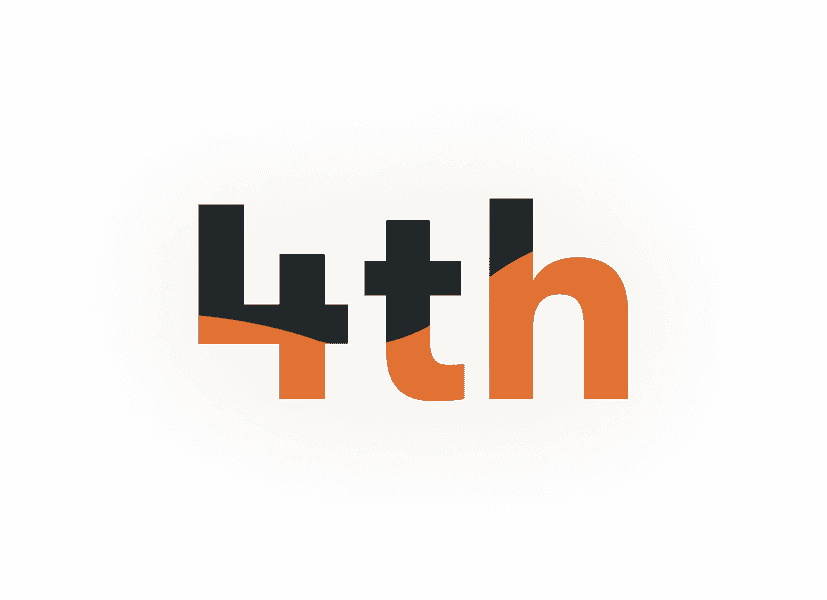
Prevention Systems
Oops, it won’t happen again. In the inevitable case that the execution in the process was misinformed, what kind of prevention is there really? Every step in a process needs to be controlled and verified or approved for the prevention of eventual mistakes to occur.
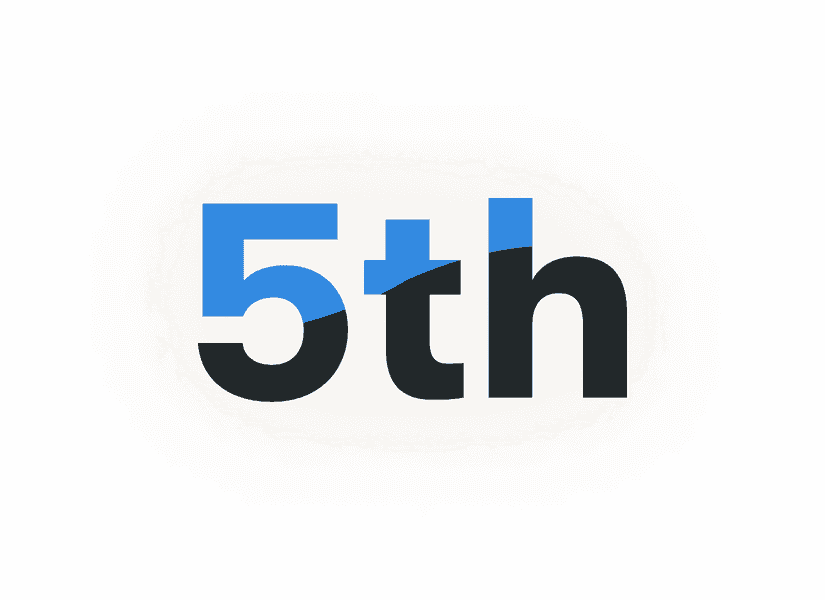